
Acknowledgements
PDS and QFD: Isis Romero
PDS And QFD
In the following PDS, crossed out values are the original PDS requirements which we did not meet
PDS:
1.Performance:
-
Easy to use
-
Quick and easy to reload staples
-
Able to use continuously (no jamming)
-
Quiet
-
Since the stapler has too much force, many of the 3D printed parts would not be able to resist the force exerted on them. Thus, we were unfortunately not able to truly test the performance. However, based on the design:
-
it is quicker to load staples since the staple holder was made more accessible
-
It is easy to use since the main functions are unchanged
-
The stapler is able to be used continuously since the jamming was due in part to a screw which restricted movement that we moved upward
2. Environment:
-
Since 3D printed techniques are usable in any temperature and if it was made of aluminum it would be as well, our product is usable in cold temperatures and hot temperatures for humans
-
Still usable after light weathering in rain, hail, snow, or dust because the parts are very resistant
-
Durable against droppage since the seals(rivets, screws) are unchanged.
3. Service Life:
-
Product runs smoothly for at least 10 years
-
Lifetime guarantee
-
Since the stapler only varies in number of parts, durability stays the same since material and seals stay the same
4. Maintenance
-
Product should only require minimal maintenance when jammed but should not jam regularly
-
Our stapler would not jam a lot but because of the tight fit and no ability to really reach any staples without a very thin wire, jamming might be an issue
-
Alternatively, because in our stapler, staples are held up from above instead of below, there is less possibility of staples getting caught on small particles so it is less likely to jam in the first place
5. Target Costs
-
Cost of manufacturing should be less than $8 for a sales price between $20 and $30
-
Our stapler costs about $16.5 to manufacture and assemble so there are less profits than expected. However, the stapler is now cheaper to manufacture than before and the stapler is very profitable
6. Competition
-
DeWalt Model #DWHTTR350
-
Stanley TR110
-
Competition is not affected by our design
7. Shipping
-
Compact for large volume shipping
-
Bulk shipping to retailers (American and international)
-
There are no special considerations in terms of shipping or fragility that would prevent these methods of transportation
8. Product Volume (Quantity)
-
1 million units/year
-
We utilized this number in all APriori calculations and this is approximately the amount the Arrow T50 sells currently. Although, the decrease in cost may later incentivize larger production rates
9. Packaging
-
Low cost
-
Able to test squeeze while in package
-
This is still achievable since changes still enable squeezing and the rest of the stapler has no external moving parts
10. Manufacturing Facilities
-
U.S. made
-
Use pre-existing facilities
-
Since the processes changed utilize the same processes used to make other parts (i.e. sheet metal folding), utilizing pre-existing facilities is possible
11. Size (Overall of Key features)
-
Handle length should provide enough torque but be comfortable to use (5 in)
-
Goal is to minimize the height and width, and target a value for the depth to provide enough torque
-
In our product, handle length was kept constant along with the height and width. (Although a previous prototype decreased the height, this change was proved unwise as the handle assembly was not able to fit snugly on the frame)
12. Weight
-
Weight of the product should not exceed 2.3 pounds
-
Weight does not exceed 2.3 pounds
13. Aesthetics
-
Looks sleek
-
Looks safe
-
Looks durable
-
Our product is all of the above although aesthetics is only slightly decreased since there is now a hole between the frame channels that slightly exposes inside parts
14. Materials
-
Metal for durability
-
Rust resistant for longevity
-
Lightweight
-
Must be lubricated internally
-
Materials were not affected in our design although because our product is a prototype, it is 3D printed and is not currently rust resistant
15. Product life span
-
10 years until reevaluation
-
Our product can still withstand 10 years since the only changes are internal and only in the number of parts and not function
16. Standards, specifications, and legal aspects
-
Must be safe to use
-
Cannot be easily weaponized
-
American standards
-
Safe to use since only one moving component is exposed on the exterior, cannot be easily weaponized for the same reason, and American standards are met
17. Ergonomics
-
Comfortable handle
-
Low force of trigger pull
-
Average hand size should be considered
-
Hand size/handle comfort was not considered since the shape of the handle was not altered. The force of the trigger pull was not affected either.
18. Customer
-
Americans in construction
-
Household Americans for everyday jobs and fliers
-
DIYers
-
International construction
-
Customers are constant since functionality is the same
19. Quality and reliability
-
Lifetime guarantee
-
Does not jam even later in product life
-
Easy to fix jamming
-
The product may jam since the space on the staple holder is relatively thin and does not allow easy access to the staples in case of jamming but very difficult to jam in the first place.
20. Shelf Life
-
Shelf life should not be a problem since the service life is so long
-
Shelf life for our product is still very long since no outside factors affect functionality because main parts are protected from external effects and does not rust
21. Manufacturing Process
-
Sheet metal stamping
-
Sheet metal bending/folding
-
Machine assembly
-
Sheet metal-transfer die
-
Stock Machining
-
Injection Molding
-
More manufacturing processes used than originally thought
22. Times scales
-
1 month market research
-
1 month design
-
2 months prototyping/testing
-
Move to manufacturing if design is improved
-
Market research took approx. 2 months
-
Prototyping/Testing took a week since the time spent on design created a good prototype
23. Testing
-
Test for no jamming
-
Weathering tests
-
Durability tests
-
Comfort test
-
Since the handle shape was not altered, comfort tests were not needed and because the material was PLA, it was not strong enough to test for no jamming. Durability and weathering tests turned out well as it took many falls with no damage.
24. Safety
-
No sharp edges on body
-
Predictable behavior when fired
-
Possible child lock/safety
-
No sharp edges as we rounded our piece yet we did not end up putting a safety as the manufacturability would have been affected
25. Company constraints
-
Must be American made
-
Must be a quality, reliable product
-
Sustainable processes
-
Plugged in only the U.S. into aPriori and since parts were merely combined, a quality product was created
26. Market constraints
-
Must have a competitive price
-
Since the cost was about $16.50, a $25 price range would bring a lot of sales as these quality products sell for up to $30
27. Patents, Literature, and product data
-
It would be good to have a patent on the mechanism for shooting out or loading staples
-
Research existing patents to avoid infringement
-
Patent is possible but would have to be filed by the existing Arrow T50 company :(
28. Political and Social implications
-
American made has political implications that can boost the American economy and increase sales
-
Our product is still all-American as we plugged only US to aPriori
29. Disposal
-
Bulk of product is metal and should be recycled
-
Plastic packaging should be recyclable
-
Plastic packaging planned is recyclable and any extra metal from this project will be a final tribute to Mack’s
Top 10 Qualities:
-
Lightweight-Our stapler is lighter than the original and below the constraint in our PDS
-
Durable-Shelf life is high and the only possible setback to a lifelong guarantee is jamming
-
Low-cost-The cost to produce this stapler is lower than the original and we decreased the piece part and fully burdened cost
-
Easy to use and reload we succeeded in doing as the staple holder is more accessible than ever as the frame is now open towards the bottom.
-
No jamming we did not consider since the staple holder has an extrusion through it which holds staples but does not have an opening to poke at staples without a really long wire
-
The noise of the stapler was not affected by our modifications
-
The stapler is as aesthetically pleasing as before however there is now an opening which may reveal some inner components which decreases aesthetics
-
Long lifespan is not affected by most of our modifications. The only possible downside would be jamming
-
Repeatability is very good in our product since the “chicken handle” immediately snaps back into place in order to staple again
-
Recyclability--Plastic packaging planned is recyclable and any extra metal from this project will be a final tribute to Mack’s
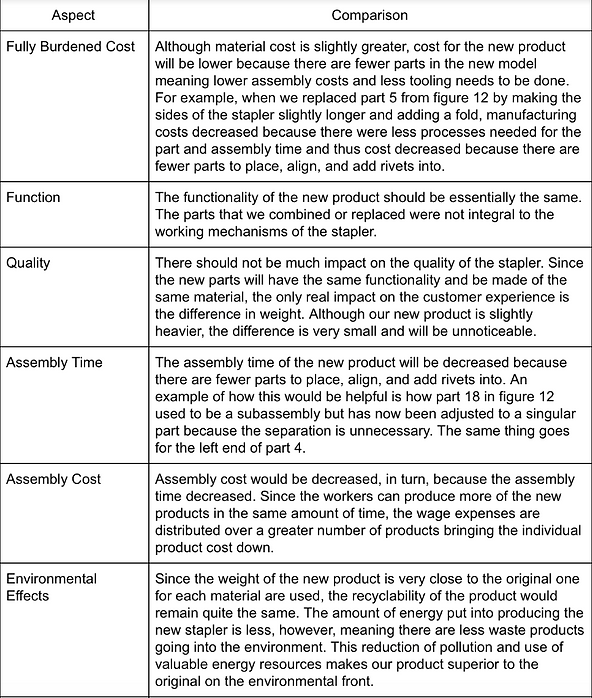
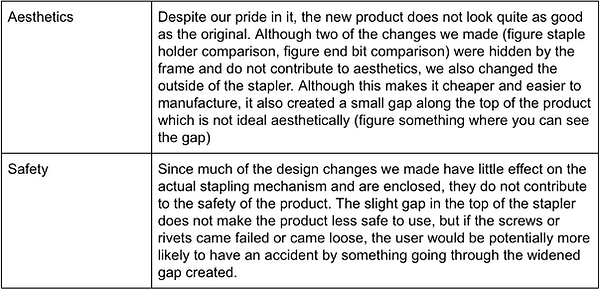
Table 5. Original vs redesigned product Comparison