Project Theme and Objectives
For our project we focused on re-designing an office stapler with the intent to make it easier to assemble and manufacture. The stapler used was Arrow T-50. We noticed that it was hard to disassemble, and it also consisted of a lot of parts. Our main objective was to reduce the number of parts; thus, we would reduce the assemble cost and time, perhaps make it lighter and easier to assemble.
Acknowledgments
Page design: Isis Romero
Bill of materials: Pierre Zivny and Gabby Yordanova
Exploded view: Pierre Zivny
Tree Analysis: Randy Janson
Competitors Comparison: Gabby Yordanova
QFD analysis: Isis Romero and Gabby Yordanova
PDS: Randy Janson and Pierre Zyvny
Initially, we only knew we needed to increase the manufacturability of the stapler. Thus, to see all of the changes, we first needed to see how the stapler worked in order to find more general objectives.


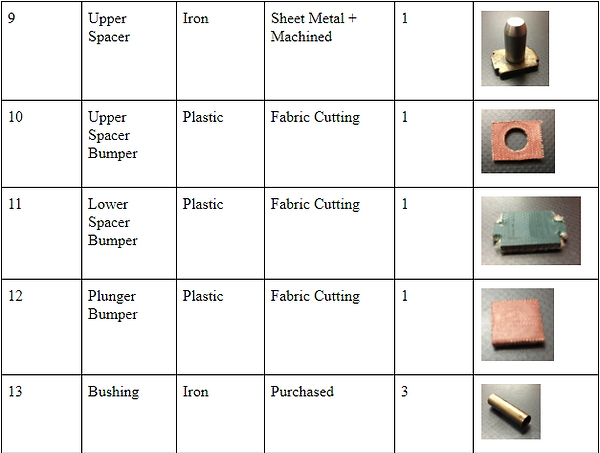

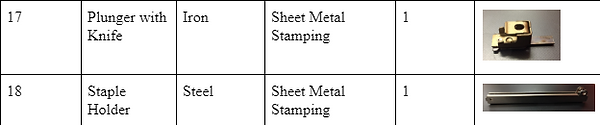

Next, we compared this product to competitors in order to create goals that will make our product the best option in staplers




These are thus the initial geometries and features we noticed were common in the staplers:
-
Sales price: $21.80 → Manufacturing cost ≈ ⅓ * 21.80 = $7.27
-
Design-for-manufacturability
-
Everything made of steel or chrome plated steel -
-
To ensure the durability of the product (improves quality)
-
Reduces manufacturing costs by being able to recycle parts to make more, smaller, parts
-
Reduces manufacturing costs by using sheet metal in bulk
-
Creates a nice smooth finish, which improves the “Look and Feel” of the object and so increases the function
-
-
Easy to remove staple holder and pusher rod assembly - this makes it quick and easy to fix jams in the stapler (improves quality)
-
Staple holder able to hold different size staples - increases usability of stapler
-
Uses purchased parts (e.g. screws and springs) so that speciality parts would not be needed as much - reduces manufacturing cost and improves quality by sourcing out parts that are specialized by other companies
-
Many of the parts can be stamped or sheet metal folded, so can be manufactured quickly and easily thus reducing manufacturing costs
-
Same thickness sheet metal so that frame channel, front cover and handle can be made from the same sheet - reduces manufacturing cost by not having to buy different sized sheets (bulk buying)
-
The two side frames are mirror images of each other, which makes manufacturing easier. Also, only few rivets connect the two, making it comparatively easy to assemble.
-
Our main goal was to increase the manufacturability of the stapler, so combining many parts in order to create a more simple geometry was a necessary objective. However, we also created a QFD in order to identify the most important qualities to alter. Here is our analysis of objectives:

We decided to include the material as part of design requirements because it has such a huge impact on the overall product although the material is not a “measurable” design requirement. However, the material would affect the other design requirements and is still a tangible specification. In fact, the material used to make the stapler is a design consideration that would change the product the most. For instance, the material would affect the weight, durability, strength and other design aspects of the stapler.
Top 3 most important design requirements:
-
Material
Material affects a lot of other design requirements, such as cost, weight, and lifespan. The cost is strongly correlated to the material used since aluminium is more expensive than steel. Also most steel staplers are actually chrome-plated, which adds to the cost. We must also consider the weight of the stapler since that is an important customer requirement (the lighter it is, the easier to use). Even though aluminum is more expensive, it is lighter. The type of material must be desirable in both parts of the most important trade off between cost and weight.
-
Handle length
Handle length affects the force required to staple since the greater the handle length the less force that must be exerted by the customer in order to create the same torque. Therefore, the greater the handle length, the greater the ease when stapling a greater number of pages together. This makes it a really important customer requirement because the ease to staple affects how much and how often it can be used for in an industrial settings. Handle length is also important for the aesthetics of the stapler and how comfortably it fits in an average user’s hand.
-
Force needed to staple
Grip force needed to staple must be considered when designing many components of the stapler. The force needed to staple affects the torque needed, the handle length, the assembled height, and the weight. Therefore by minimizing the force we must carefully target the weight, height, and length. We can’t just consider cost into picking those dimensions because any increase in force needed to staple would make it harder for customers to use since they won’t be able to get through hard materials easily or staple as many objects together without significantly more effort.
Considering our QFD findings, the areas to concentrate our design are the following:
-
Cost
Ways we can decrease cost involve making it easier to manufacture or assemble. One way we can achieve that is by reducing the number of parts. Looking at the bill of materials, we noticed that it is possible to combine the front cover and the frame channels. Perhaps, we can have 2 bigger frame channels that include the functionality of the front cover. Even though both parts are made by sheet metal stamping, and we can’t eliminate the cost of the tool, we will still be able to decrease time for manufacturing and assembly, which should decrease cost.
-
Easy to use and reload
Factors that affect how easy it is to use include the dimensions of the stapler, the handle length, and the weight. We have to make sure we target their sizes. The handle and width should comfortably fit the palm of an average user. Also, we can decrease the weight a little bit by combining parts.
3. Handle length and force exerted by staple
We can increase the handle length so that the customer exerts less force on the stapler to get the same torque (Force times perpendicular distance). The handle length also affects the comfort of the customer since the customer will ultimately have to grip the handle in order to use the stapler. We could also focus on increasing the force exerted by the stapler so that the stapler can be used on harder surfaces or on a greater volume of papers.
Then, we created a PDS analysis so we could figure out the constraints necessary for our product: This can be seen in a separate Tab
Finally, we created a cost analysis from the original product in order to see how much money our product should cost. (Our product should save money, and thus be below this number). In the following table, we can see the cost of only the relevant pieces that ended up being altered by our design.
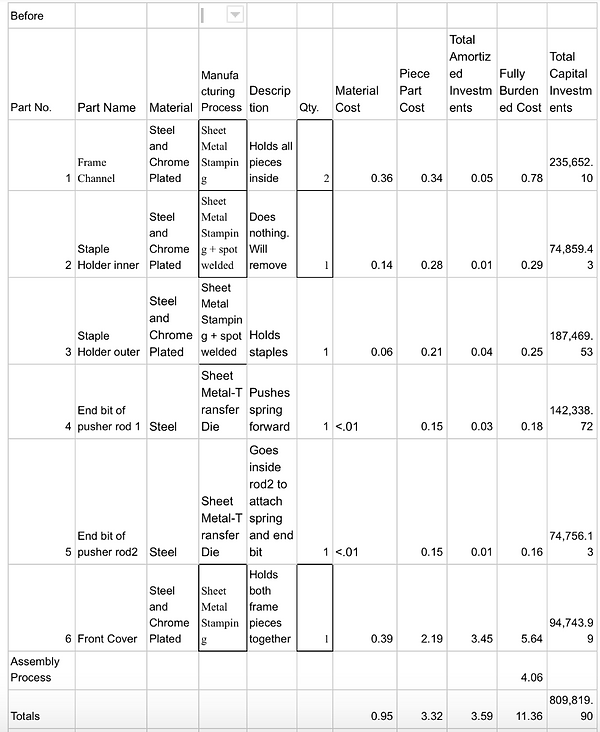
Conclusions about manufacturing cost analysis:
Another VPE does not apply to us, although one from China would decrease costs by 50%, because our company prides itself on being All-American Made. Bigger tolerances or less accuracy decreases costs since the overall effect is that the parts can be machined with more freedom and thus less time is spent machining and aligning. Our highest cost components are the front cover, which we are combining into the frame channel in order to reduce cost, and the staple holder, which we might combine into the frame channel as well. Since the fully burdened costs are relatively low and the total capital investments are also low compared to expected profits, this chart may be analyzed as correct. This cost analysis proves that our initial ideas about combining part may have an overall positive effect in reducing part cost. We have correctly identified the highest cost components.